Self-priming pumps are clever devices that automatically draw liquid without manual priming. They use centrifugal force to create a partial vacuum, allowing them to handle liquids from depths up to 10 meters. These pumps start with liquid inside and expel air while drawing more fluid, making them ideal for various applications.
You’ll find them in agricultural irrigation, construction dewatering, wastewater management, and even firefighting.
They’re versatile, efficient, and can handle fluids with gas bubbles. While they have some limitations, like a maximum priming height, their advantages often outweigh the drawbacks.
If you’re curious about the nitty-gritty details, there’s plenty more to discover about these handy pumps.
Key Takeaways
- Self-priming pumps automatically draw liquid without manual priming, using centrifugal force to create a partial vacuum.
- They can handle liquids from depths up to 10 meters and are designed to prevent backflow.
- Applications include agricultural irrigation, dewatering, wastewater management, chemical processing, and firefighting operations.
- Advantages include versatility with air-containing fluids, consistent flow rates, and reduced maintenance time and costs.
- Operational considerations involve assessing priming height, fluid viscosity, and ensuring the suction line is free from air leaks.
What Is a Self-Priming pump?
A self-priming pump is a versatile piece of equipment that can automatically draw liquid into its system without manual priming. You’ll find these pumps particularly useful in situations where the liquid level fluctuates or when you’re dealing with fluids that contain air or gas.
The self-priming ability of these pumps is what sets them apart from conventional pumps.
Here’s how it works: The pump uses centrifugal force to create a partial vacuum, which allows it to pull liquid up from a lower level. This priming process happens automatically, making your pumping operations more efficient and hassle-free. You won’t need to worry about constantly refilling the pump or dealing with air locks.
Self-priming pumps can handle liquids from depths of up to 10 meters, depending on factors like altitude and temperature. They’re designed with built-in mechanisms to prevent backflow and maintain their primed state, which means less maintenance for you.
Whether you’re working in agriculture, construction, or wastewater management, a self-priming pump can be a real game-changer, helping you move liquids more effectively and with less downtime.
Are Centrifugal Pumps Self-Priming?
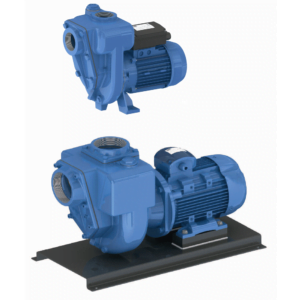
Standard centrifugal pumps aren’t self-priming. They lack the necessary seals between suction and discharge to evacuate air from the suction line, which is crucial for self-priming operation.
Centrifugal pumps are commonly used in large-scale wastewater treatment plants due to their efficiency in handling high volumes of fluid, but they typically require additional modifications for self-priming capabilities.
For a centrifugal pump to work effectively, it typically needs a flooded suction. This means you’ve got to have the liquid at or above the pump level before starting it up. It’s a bit like needing to prime your car’s engine before a long trip – the pump must have liquid to get going.
You can make a centrifugal pump self-priming by surrounding it with a tank of liquid, but this setup’s main purpose is to ensure lubrication and cooling during operation. It’s not quite the same as a true self-priming pump.
Some manufacturers have developed self-priming centrifugal pump designs, but these often involve additional components to help evacuate air and maintain performance.
How Do Self-Priming Pumps Work?
Self-priming pumps’ inner workings are a marvel of engineering ingenuity. These clever devices start with a bit of liquid already inside, which is key to their operation.
When you turn on a self-priming pump, its impeller begins to spin rapidly, creating a whirlwind of action inside the pump casing. As the impeller rotates, it creates a partial vacuum that draws a mixture of air and liquid into the pump. This mixture is then forced through the pump, with the air being expelled and the liquid flowing back down.
It’s like a mini cyclone in your pump! The process continues until all the air is removed from the suction line, allowing atmospheric pressure to push the liquid up into the pump.
Once primed, these pumps keep the liquid flowing smoothly. They’re equipped with check valves that prevent air from sneaking back in, ensuring consistent operation.
This clever design allows self-priming pumps to handle liquids with gas bubbles and varying fluid levels, making them incredibly versatile. Whether you’re dealing with wastewater, irrigation, or chemical processing, these pumps have got you covered!
Common Applications for Self Priming pumps
From construction sites to chemical plants, self-priming pumps find countless applications across diverse industries.
You’ll often see these versatile pumping solutions in action in agricultural irrigation systems, where they efficiently draw water from various sources to keep crops hydrated. In construction, they’re invaluable for dewatering operations, ensuring that excavations and work areas stay dry and manageable.
Self-priming pumps also play a crucial role in wastewater management. They’re adept at handling sewage and sludge in treatment plants, contributing to environmental protection efforts.
In the chemical processing industry, you’ll find these pumps transferring corrosive substances safely and efficiently.
But that’s not all – self-priming pumps are also heroes in firefighting operations. They can quickly draw water from natural sources or hydrants, providing the high-pressure flow needed to combat fires effectively.
Whether you’re dealing with variable water sources, solid particles, or air pockets, these pumps have got you covered. It’s no wonder they’ve become go-to solutions in so many fields – they’re like the Swiss Army knives of the pumping world!
Our Self-Priming Pump Solutions
-
GT Self Priming Solids Handling Dirty Water Electric Pump£478.20 – £608.32Price range: £478.20 through £608.32 +VAT
Things to Consider When Selecting a Self-Priming Pump
Selecting the right self-priming pump for your application involves carefully considering several crucial factors.
First, you’ll need to assess the maximum priming height required, which typically shouldn’t exceed 10 meters for water. Remember, this can vary depending on the liquid and environmental conditions you’re dealing with.
Next, consider the viscosity of the fluid you’re pumping. Higher viscosities can affect flow rates and require specialised pumps for thicker liquids.
Don’t forget to evaluate the size and nature of any solids present in your fluid. Larger particles can lead to clogging, so you might need a pump that’s built to handle debris.
Here are three key points to keep in mind:
- Ensure your suction line is free from air leaks
- Check the available installation space for the pump and its components
- Match the pump’s capabilities to your specific application needs
Advantages of Self-Priming Pumps
Harnessing the power of self-priming technology, these pumps offer numerous advantages that make them indispensable in various industries. You’ll find that self-priming pumps eliminate the need for external priming systems, saving you time and money on maintenance.
They’re particularly handy when dealing with fluids that contain air or gas, making them versatile for a wide range of applications.
One of the standout benefits is their ability to maintain consistent flow rates without interruption. This means you won’t have to worry about pump failure due to air pockets or intermittent supply.
Plus, you can install these pumps above the liquid source, giving you more flexibility in your setup.
The built-in mechanisms of self-priming pumps create a vacuum that continuously evacuates air, reducing the priming time and ensuring reliable performance.
This clever design minimises the risk of cavitation, which can be a real headache in other pump types.
By automatically drawing fluid into the pump, they’re ready to go when you need them, making your operations smoother and more efficient.
It’s no wonder these pumps have become a go-to solution across industries!
Disadvantages of Self Priming Pumps
While self-priming pumps offer numerous advantages, they’re not without their drawbacks. You’ll need to consider a few key limitations before deciding if they’re right for your application.
For starters, these pumps require an initial priming liquid to get going, which can be a problem if you’re working in completely dry conditions or don’t have a startup liquid handy.
Another important factor to keep in mind is the maximum theoretical self-priming height. For water, it’s about 10 meters, but this can vary depending on the liquid and environmental conditions. You’ll want to ensure your setup falls within these limits for optimal performance.
Here are three more disadvantages to consider:
- Air leaks in the suction line can seriously hamper the pump’s ability to draw fluid.
- Larger self-priming pumps may not fit in tight spaces, limiting their use in some environments.
- Extended periods of running dry can damage the pump, potentially leading to costly repairs or replacements.
Lastly, remember that careful monitoring is crucial to prevent overheating and equipment failure.
While self-priming pumps are versatile, these drawbacks are worth weighing against their benefits for your specific needs.
Frequently Asked Questions
How Long Can a Self-Priming Pump Run Dry?
Self-priming pumps should not run dry for more than 5-7 minutes at a time. While these pumps are designed to operate temporarily without liquid, extended dry running can cause:
- Mechanical seal damage
- Excessive heat buildup
- Premature wear on pump components
- Potential pump failure
Best practices for dry running:
- Monitor the pump during priming
- Install dry run protection devices
- Stop the pump if it hasn’t primed within 5 minutes
- Allow cooling between priming attempts
- Check for air leaks if priming takes too long
Note: Specific dry-run time limits may vary by manufacturer and pump model. Always consult the manufacturer’s manual for exact specifications.
What Is the Difference Between a Self-Priming Pump and a Pressure Pump?
You’ll find that self-priming pumps create a vacuum to draw liquid, even with air present. They’re great for above-ground use. Pressure pumps, however, need a constant liquid supply and can’t handle air. They’re better for maintaining pressure.
Where are self-priming pumps used?
Self-priming pumps are commonly used in:
- Water transfer applications where the pump is located above the water source
- Swimming pool circulation systems
- Agricultural irrigation
- Marine applications and bilge pumping
- Municipal water and sewage systems
- Industrial processes requiring fluid transfer
- Dewatering operations
- Fire protection systems
- Construction sites for water removal
- Garden and landscape irrigation systems
These pumps are particularly valuable in situations where:
- Manual priming would be impractical or inconvenient
- The pump needs to remove air from the suction line
- There’s a risk of losing pressure
- The liquid source level fluctuates
What are the applications of self priming pumps?
Self-priming pumps have numerous applications:
- Water Supply and Distribution
- Municipal water systems
- Residential water supply
- Irrigation systems
- Swimming pools and water features
- Industrial Processes
- Chemical transfer
- Wastewater treatment
- Food and beverage processing
- Paint and coating applications
- Construction
- Dewatering operations
- Site drainage
- Foundation pit pumping
- Emergency flood control
- Marine Applications
- Bilge pumping
- Engine cooling systems
- Deck washing
- Ballast transfer
- Agriculture
- Field irrigation
- Livestock watering systems
- Crop spraying
- Waste handling
- Mining
- Mine dewatering
- Slurry transfer
- Process water handling
- Dust suppression
- Emergency Services
- Fire fighting
- Flood response
- Emergency water supply
- Disaster relief operations
- Utilities
- Utility maintenance
- Sewage transfer
- Storm water management
- Power plant cooling systems
How to tell if a pump is self-priming?
A pump is self-priming if:
- It has a built-in check valve or foot valve
- The pump’s manual specifically states it’s self-priming
- It can create suction and move liquid upward without manual priming
- It includes an integrated priming chamber or reservoir
You can confirm a pump is self-priming by checking:
- The pump housing has a dedicated priming chamber
- Product specifications list “self-priming” capabilities
- The maximum suction lift height is specified
- The pump can restart automatically after running dry
Non-self-priming pumps typically:
- Need external priming assistance to start
- Require manual filling before operation
- Must be positioned below the liquid level
- Cannot create initial suction independently
Conclusion
You’ve now explored the world of self-priming pumps, understanding their mechanics and applications. These versatile devices offer solutions for challenging pumping scenarios, from wastewater management to irrigation. As you consider your next project, remember the advantages and limitations of self-priming pumps. They’re not always the best choice, but when you need reliable fluid handling above the source or with intermittent supply, they’re often your go-to option. If you have any questions about Self Priming Pumps get in touch with the team at AES Rewinds.